Why IoT Is Paving the Way for Predictive Maintenance
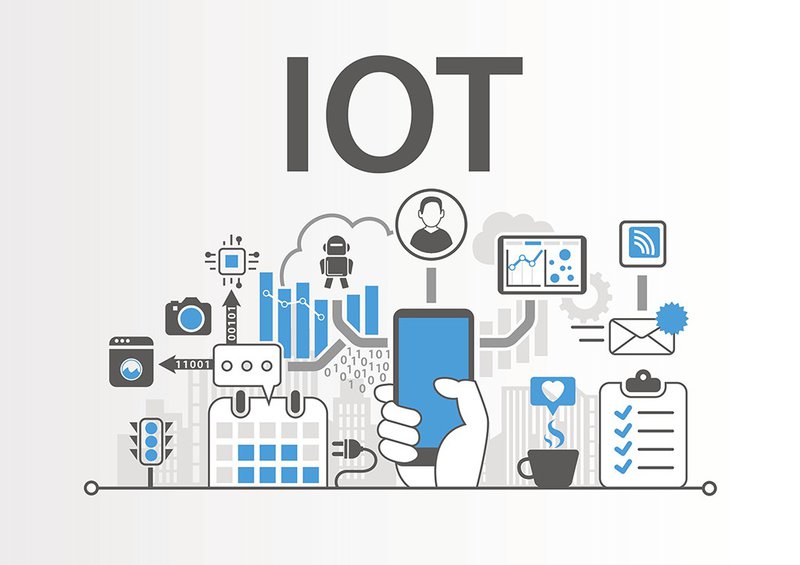
Are you tired of unexpected equipment breakdowns causing costly downtime? Look no further, because IoT is here to pave the way for predictive maintenance. With IoT, you can proactively monitor your machinery’s health and predict when maintenance is needed, saving you time and money.
In this article, we will explore the role of IoT in predictive maintenance, the benefits it offers, key technologies driving IoT-based maintenance, real-life examples, challenges, and future trends.
So, get ready to embrace the power of IoT and revolutionize your maintenance practices.
Key Takeaways
- IoT revolutionizes monitoring and servicing of equipment
- Predictive maintenance with IoT improves efficiency and cost savings
- IoT enables real-time data collection for performance monitoring
- IoT helps identify potential issues before they become major problems
The Role of IoT in Predictive Maintenance
The role of IoT in predictive maintenance is crucial for improving operational efficiency and reducing downtime. With the advancements in technology, IoT has become an integral part of maintenance strategies.
One key aspect is the role of sensors in collecting real-time data from machines and equipment. These sensors continuously monitor various parameters such as temperature, pressure, and vibration. By analyzing this data through data analytics, patterns and anomalies can be identified, allowing for predictive maintenance actions to be taken proactively.
This means that potential issues can be addressed before they cause significant disruptions or failures. By leveraging IoT and the role of sensors in predictive maintenance, organizations can optimize their maintenance schedules, decrease equipment downtime, and ultimately increase productivity and cost savings.
Benefits of Implementing IoT for Predictive Maintenance
When it comes to reducing downtime, implementing IoT in your maintenance processes can be a game-changer.
With real-time data and analytics, you can identify potential issues before they become major problems, allowing you to schedule maintenance proactively and avoid costly downtime.
Additionally, IoT can improve equipment performance by monitoring key metrics and providing insights that can help optimize operations and increase efficiency.
Reduced Downtime Through Iot
By using IoT, you can minimize downtime through predictive maintenance. Implementing IoT technology in your company allows you to monitor equipment in real-time, identify potential issues before they cause a breakdown, and schedule maintenance proactively. This proactive approach significantly reduces downtime and its associated costs.
With IoT, you can collect and analyze data from various sensors and devices, enabling you to gain valuable insights into your equipment’s health and performance. By leveraging data analytics, you can identify patterns and trends that indicate potential failures or maintenance needs. This enables you to take timely action, preventing unexpected breakdowns and reducing the need for reactive maintenance.
Overall, IoT empowers you to optimize your maintenance operations, reduce costs, and ensure uninterrupted productivity.
Improved Equipment Performance With Iot
Implementing IoT technology in your company can enhance equipment performance. By allowing you to monitor and analyze data in real-time, IoT enables proactive maintenance. Improved equipment monitoring through IoT provides valuable insights into the condition of your equipment. This enables you to identify potential issues before they become major problems. Continuous monitoring of key parameters such as temperature, vibration, and energy consumption helps detect anomalies. Immediate action can then be taken to prevent breakdowns or failures. IoT also enables maintenance teams to receive real-time notifications and alerts. This ensures that issues are addressed promptly. This proactive approach not only reduces downtime but also extends the lifespan of your equipment. By leveraging IoT for equipment performance monitoring, you can optimize operations, minimize disruptions, and ultimately increase productivity and profitability.
Key Technologies Driving IoT-based Predictive Maintenance
To understand the key technologies driving IoT-based predictive maintenance, you need to explore the role of machine learning and data analytics. These emerging technologies are at the forefront of revolutionizing maintenance practices.
Machine learning algorithms analyze vast amounts of data collected from IoT sensors to identify patterns and anomalies. This allows for the prediction of equipment failures before they occur, enabling proactive maintenance strategies.
Data analytics plays a crucial role in processing and interpreting this data, providing valuable insights into equipment performance and health.
By leveraging these key technologies, organizations can optimize maintenance schedules, reduce downtime, and maximize operational efficiency.
With IoT-based predictive maintenance, you can stay one step ahead by harnessing the power of machine learning and data analytics to ensure the reliability and longevity of your equipment.
Real-life Examples of Successful IoT-driven Predictive Maintenance
One way organizations have successfully revolutionized their maintenance practices is by harnessing the power of machine learning and data analytics to predict and prevent equipment failures. By leveraging IoT-enabled sensors and real-time data, companies are able to monitor the health of their machines and identify potential issues before they become major problems. This proactive approach to maintenance has resulted in significant cost savings and improved overall efficiency.
Here are some successful case studies of organizations that have implemented IoT-enabled maintenance:
Organization | Industry | Results |
---|---|---|
Company A | Manufacturing | Reduced downtime by 30% |
Company B | Energy | Decreased maintenance costs by 25% |
Company C | Transportation | Increased equipment lifespan by 20% |
Company D | Healthcare | Improved patient safety by 15% |
These examples highlight the power of IoT in transforming maintenance practices and delivering tangible benefits to organizations across various industries. By embracing IoT-enabled maintenance, companies can proactively address equipment failures and optimize their operations for greater success.
Challenges and Solutions in Adopting IoT for Predictive Maintenance
Facing challenges in adopting IoT for predictive maintenance? You can overcome these obstacles by ensuring proper integration of machine learning algorithms, establishing reliable data connectivity, and training your workforce on new technologies.
Challenges in implementation can arise from the complexity of IoT systems and the need to integrate them with existing infrastructure. Data security concerns are also a major challenge, as IoT devices generate vast amounts of data that need to be protected from unauthorized access.
By properly integrating machine learning algorithms, you can effectively analyze the data collected from IoT devices and make accurate predictions for maintenance needs. Establishing reliable data connectivity ensures that the data collected is transmitted in real-time, enabling timely maintenance actions.
Lastly, training your workforce on new technologies equips them with the skills needed to effectively utilize IoT for predictive maintenance.
Future Trends in IoT-enabled Predictive Maintenance
In this discussion, you will explore the benefits of predictive maintenance, the role of IoT in maintenance, and the emerging technologies that are revolutionizing the field.
You will learn how predictive maintenance can help you minimize downtime, reduce costs, and improve overall efficiency. Additionally, you will discover how IoT is enabling real-time monitoring and data analysis, allowing for proactive maintenance and enhanced decision-making.
Finally, you will gain insights into the latest technologies, such as artificial intelligence and machine learning, that are transforming maintenance practices for greater effectiveness and reliability.
Benefits of Predictive Maintenance
The benefits of predictive maintenance include reducing downtime and increasing equipment lifespan. By implementing predictive maintenance strategies, you can experience improved efficiency and significant cost savings.
Here are some reasons why you should consider predictive maintenance for your equipment:
- Peace of mind: With predictive maintenance, you can proactively identify and address potential issues before they become major problems, giving you peace of mind and minimizing the risk of unexpected breakdowns.
- Optimized performance: By continuously monitoring and analyzing equipment data, you can optimize performance and ensure that your equipment is operating at its peak efficiency, leading to improved productivity and output.
- Extended equipment lifespan: Regular maintenance and early detection of issues can help extend the lifespan of your equipment, saving you money on replacement costs in the long run.
- Reduced maintenance costs: Predictive maintenance allows for better planning and scheduling of maintenance activities, reducing the need for costly emergency repairs and minimizing overall maintenance expenses.
Incorporating predictive maintenance into your operations can bring about significant improvements in efficiency and cost savings, providing a competitive advantage in today’s fast-paced business environment.
Iot’s Role in Maintenance
Implementing IoT technology in maintenance operations can revolutionize the way you monitor and service equipment. This can lead to improved efficiency and cost savings. By integrating IoT in your maintenance workflows, you can experience significant benefits in terms of cost reduction.
IoT devices can collect real-time data from your equipment. This allows you to monitor its performance and identify potential issues before they become major problems. With this predictive maintenance approach, you can schedule maintenance activities proactively. This helps avoid costly breakdowns and minimizes downtime.
Furthermore, IoT-enabled sensors can provide valuable insights into equipment usage and performance. This helps you optimize maintenance schedules and reduce unnecessary service visits.
Emerging Technologies for Maintenance
Now that you understand the role of IoT in maintenance, let’s dive into the emerging technologies that are revolutionizing the field.
One of the key advancements is the use of smart sensors, which are transforming how we monitor and track equipment performance. These sensors gather real-time data about temperature, pressure, vibration, and other crucial parameters, providing a wealth of information for analysis.
Harnessing the power of data analytics is another game-changer in maintenance. By leveraging advanced algorithms and machine learning, organizations can identify patterns and anomalies in the sensor data, enabling them to predict and prevent equipment failures before they occur. This proactive approach not only minimizes downtime and maintenance costs but also enhances overall operational efficiency.
Incorporating smart sensors and data analytics in maintenance brings several benefits:
- Improved equipment reliability
- Enhanced safety for workers
- Increased productivity and operational efficiency
- Cost savings through optimized maintenance schedules
These technologies are paving the way for a more proactive and efficient maintenance approach, ensuring smooth operations and minimizing disruptions.
Frequently Asked Questions
What Are the Potential Risks or Drawbacks of Implementing Iot for Predictive Maintenance?
When implementing IoT for predictive maintenance, there are potential risks and drawbacks to consider. These include increased vulnerability to cyberattacks, data privacy concerns, and the cost of implementing and maintaining the necessary infrastructure.
How Does Iot Technology Help in Reducing Maintenance Costs?
By using IoT technology, you can reduce downtime and increase efficiency. IoT allows for real-time monitoring of equipment, enabling you to detect issues before they become major problems, ultimately reducing maintenance costs.
Can You Provide Some Specific Examples of Industries or Sectors That Have Successfully Adopted Iot for Predictive Maintenance?
Industries or sectors that have successfully adopted IoT for predictive maintenance include manufacturing, transportation, and energy. They have seen improved efficiency, reduced downtime, and cost savings through real-time monitoring and data analysis.
What Are the Key Challenges That Organizations Face When Adopting Iot for Predictive Maintenance, and How Can They Overcome Them?
Key challenges in IoT adoption for predictive maintenance include data security, connectivity issues, and lack of skilled workforce. Overcome these challenges by implementing robust security measures, investing in reliable connectivity solutions, and providing training to employees.
What Are Some Emerging Trends or Advancements in Iot-Enabled Predictive Maintenance That We Can Expect to See in the Future?
In the future, you can expect to see advancements in IoT-enabled predictive maintenance. By overcoming challenges in implementing IoT for predictive maintenance, organizations will benefit from improved efficiency and reduced downtime.